For decades, the construction of above ground storage tanks has relied on butt welded steel tanks as a mainstay.
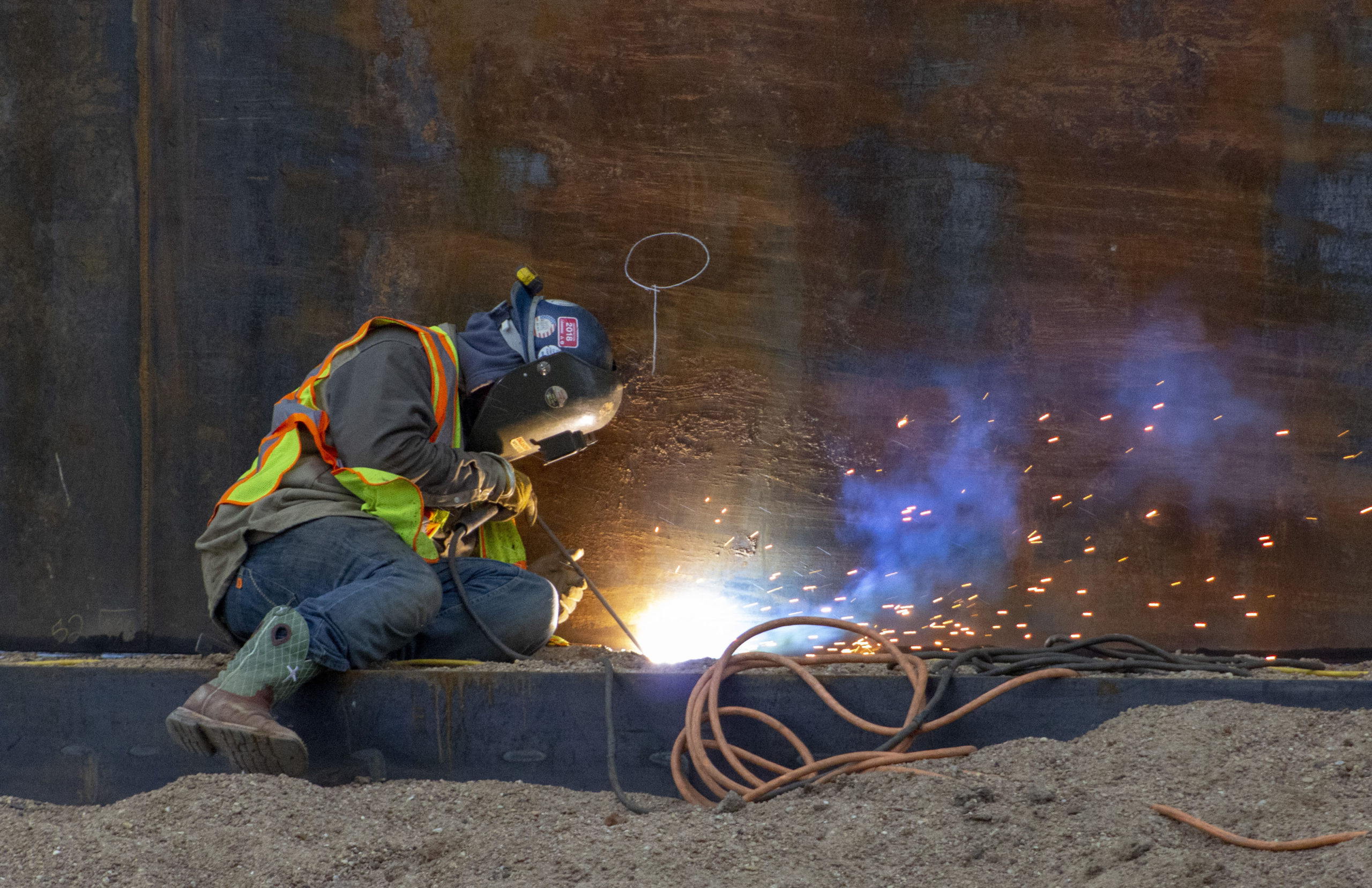
Around 1936, welded steel tanks replaced riveted tanks in new above ground storage tank construction. With this change, API standards were introduced to guide construction for safety and economy. API 650, now in its thirteenth edition, sets the standard for welded steel tanks, covering materials, design, fabrication, erection, welding, and inspection.
Between 1960 and 1990, older riveted tanks transitioned to welded tanks. However, after a catastrophic failure in 1986, the economic appeal waned. In 1991, the API 653 Standard addressed criteria for dismantling and reconstructing tanks, as well as inspections, repairs, and alterations.
In building welded steel above ground storage tanks, various welding processes are used.
The leading welding process, commonly known as stick (arc) welding or Shielded Metal Arc Welding (SMAW), has been and still is very common today for the construction of above ground storage tanks. The SMAW process is versatile and very well suited to the environment of field erected work.
In the early 1980s, the tank industry adopted Submerged Arc Welding (SAW) as a popular method. This process was utilized for lap welded bottoms and roofs as well as butt welded shell joints. Developing a method of welding that would ensure cleanliness of porosity under the surface of the weld took many years of education.
Many tank builders abandoned this method of welding on bottoms due to the inability to control moisture from the bottom side of the lap plates. However, the use of preheat in the winter time has made welding the girth (round) seams connecting one shell course to the next very successful. This method of welding, known as Three O’Clock welding (3-O’Clock), delivers good clean and smooth penetration and provides a more uniform weld. The submerged arc weld blends and merges well with the two plates being joined and also provides X-ray quality welds.
API 650 section 9 mandates that all welding on above ground storage tanks must adhere to the manufacturer’s Weld Procedure Specifications (WPS) and the supporting Procedure Qualification Record (PQR). Welding operators undergo testing and certification following the tank builder’s welding procedures. Newly constructed above ground storage tanks undergo various types of inspection for their welds.
Radiographic (x-ray) testing confirms the compliance of welding operators with the welding procedure. This method is applied to shell butt weld joints, annular plate butt joints, and flush type connections with butt joints. However, it is not utilized for bottom and roof lap joints, top angle joints, man-way necks, shell to bottom joints, structural joints, and appurtenances.
Welds undergo assessment based on ASME Section VIII standards, categorized as either acceptable or unacceptable. API 650 Section 8 outlines criteria for determining the number of shots required for each welding operator, considering factors such as thickness, number of shell courses, number of T joints, and linear feet of vertical and horizontal welds completed. The storage tank owner/operator retains the right to choose x-ray locations based on the criteria outlined in Section 8.1.2.
Tank shell welds should undergo cleaning and visual inspection from both sides of the joint to ensure they are free of defects such as craters, pinholes, undercut, and underfill.
Excessive weld reinforcement or overlay should be ground smooth, along with the removal of all arc strikes, weld spatter, fit-up, and scaffold strap burrs. This process includes replacing any parent metal that might have been lost in the process of removing the bracket straps, nuts, and fit-up equipment.
The most common method of testing tank floor weld seams for leaks is Vacuum Box Testing. Before performing the vacuum testing, it is essential to visually inspect all floor welds to ensure they are complete and free of any slag, weld burrs, and other defects such as pinholes, undercut, and underfill.
Similarly, the shell-to-floor/bottom joint undergoes visual inspection in the same manner. Upon completing one side of the welded joint, a common weld test involves applying a high flash point penetrating fluid, such as diesel fuel, to the opposite side. The welded side is then checked for any visible signs of wicking. If repairs are necessary, the penetrating fluid test is repeated before welding the other side.
Appurtenances, including inlet and outlet nozzles, should also undergo a thorough visual check to ensure welds are free of defects. Air pressure is then applied through a quarter-inch pipe threaded tell-tale hole in the re-pad. Soap suds are brushed or sprayed onto all sides of the re-pad and both sides of the penetration where the weld attaches the pipe nozzle to the shell. The welds are visually inspected for small air bubbles penetrating the soap solution.
Once the welds pass inspection, the tank is deemed ready for service. Similar inspection methods are employed for weld repairs throughout the tank’s lifetime.
If you have any storage tank weld questions, contact us at 800-774-3230 or through our website.